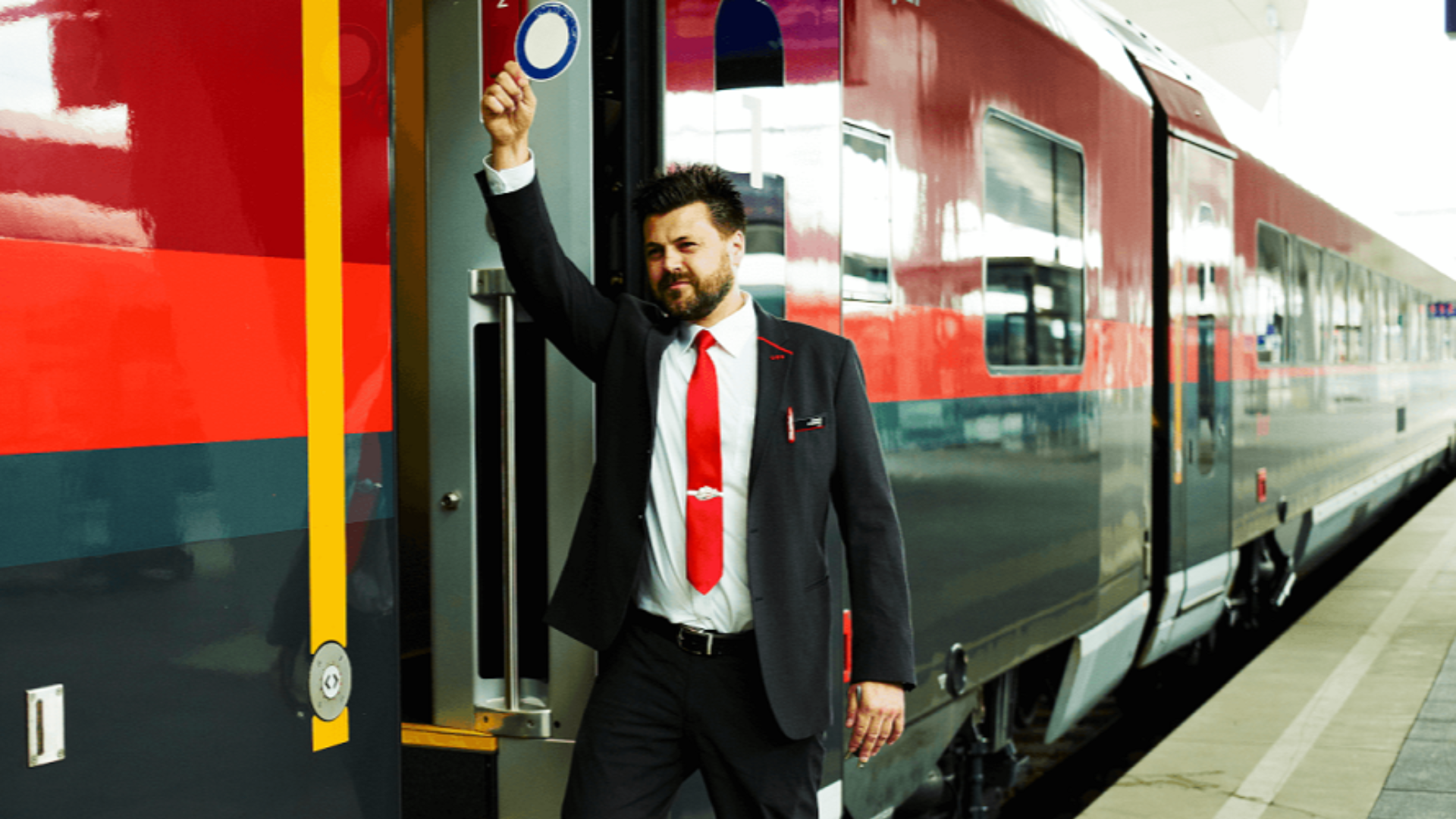
Case ÖBB – Procurement of complex product groups
ÖBB’s employees use a new software solution for the procurement of their work tools, including workwear. The approval process is also automated, so the employees receive their orders even faster and costs had been significantly reduced.
Challenge
Automation of the complete procurement pro- cess. System-based order availability of complex product groups. Simplification and standardizing of the approval and signature processes.
Solution
All order and procurement processes are handled consistently. Deli- very confirmations, invoices, credit notes, contracts, and catalogs are electronically available. The automated procurement of uniforms and protective clothing includes 30 categories as well as sizes and colors.
”We feel very well supported in our efforts to reduce bureaucracy and to improve the usability of the solution for employees. We were provided with a well-suited platform to implement this ambitious project.”
Anton Bruckner, ÖBB
10,000 suppliers offer 650,000 articles to 40,000 employees
The ÖBB procurement department coordinates and controls all procurement processes and purchasing activities. The following facts and figures illustrate the scope of this task: The supplier management activities include about 10,000 suppliers and 2,500 contracts. The employees are provided with 650,000 different order items in more than 750 product groups.
Less bureaucracy and simple and fast processes
ÖBB implemented the web-based Online Product Catalog (OPC) of OpusCapita as the central procurement platform. All 40,000 employees now have access to a consistent procurement process, regardless of whether they are office or mobile workers. The dynamic search, filter, and sorting options and the menu display support the intuitive handling.
Workwear in all variations and sizes
One of the most important steps was the go-live of the system-based order function for workwear and protective clothing. This was also the biggest challenge because 30 categories, sizes, and colors must be recorded. Permissions are stored in the system so that uniforms and protective clothing can only be ordered according to the employee’s work and quota, removing the authorization requirement.
Automated approvals and signatures
With the automating and standardizing of the multistage approval steps, the procurement of the equipment has been simplified and accelerated for all employees. In addition, the orders are automatically signed and transmitted directly to the supplier. After receiving the order, the employee confirms the goods receipt with just one click. After this, the transmission and the goods receipt are done automatically in the SAP system. There are also stock-held items that need to be available frequently and quickly. For these products, the billing takes place internally.

About ÖBB
ÖBB (Österreichische Bundesbahnen) is Austria’s largest mobility services provider. The Group transports 458.9 million passengers and 110.6 million tons of goods to their destinations every year in an eco-friendly manner.